June 25, 2015 weblog
Blade supercar has bi-fuel engine, signifies 3D-print platform
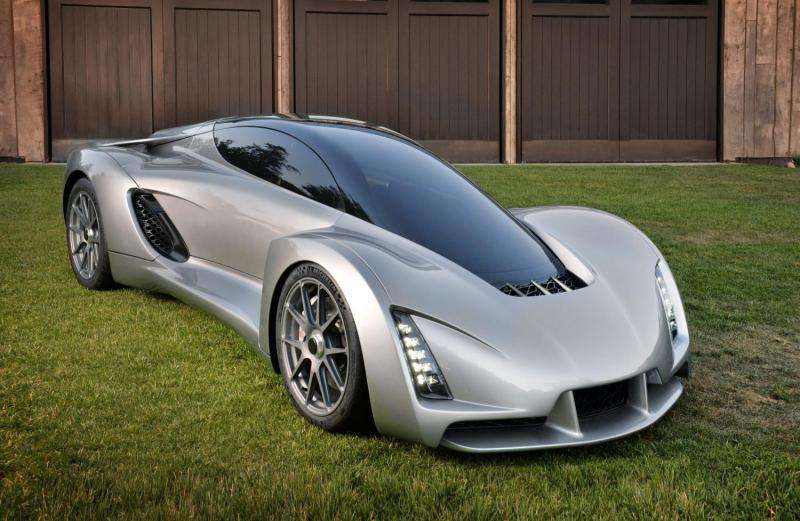
Divergent Microfactories made a name for itself this week with a twin announcement of its supercar prototype and the business platform underlying the car. It's all about 3D printing and the claims are impressive.
The company announced they have built the world's first 3D-printed supercar Blade. The total weight of the car is 1,388 pounds; it goes from 0 to 60 in about two seconds. Engine? The car uses a 700 HP, 4-cylinder turbocharged internal combustion engine fueled by compressed natural gas or gasoline.
The other part of the announcement was its business intention and technology platform. Divergent Microfactories CEO Kevin Czinger has introduced the company's plan to "dematerialize and democratize" car manufacturing.
His goal is not to have his own company name behind volume manufacturing but to put the platform in the hands of small entrepreneurial teams around the world. He would like to make a difference in offering a sustainable manufacturing platform for the future. Czinger thought the result could be "a renaissance in car manufacturing." They could set up their own microfactories and build their own cars and, eventually, other large complex structures.
That way, innovation could be made affordable; the technology could help reduce health and environmental impacts of traditional manufacturing.
Forbes said, "Czinger isn't committed to doing all the manufacturing himself. He says his new company, Divergent Microfactories, is more interested in licensing its 3-D-printing technology to a new generation of relatively small automakers around the world."
Talking about the business plan, Czinger said,: "we will provide the necessary tools for people to set up a microfactory, and the technologies to allow them to build vehicles. We will also sell a limited number of high performance vehicles that will be manufactured in our own microfactory."
Czinger's arguments: The industry has succeeded in making greener cars but the manufacturing process, with its resource use and generated pollution, is anything but environmentally friendly. The Blade is lighter than traditional vehicles but has strength and durability. A stronger, lightweight vehicle would mean less wear on roads and fewer accident fatalities. What is more, vehicles built by smaller local teams reduce costs, time, and enhance quality. His approach would cut materials, cut the energy use, cut the pollution and cut the cost of car manufacturing,
His primary tools are 3D-printed nodes connected by carbon fiber tubing for a chassis that is assembled in minutes. The FAQ section of the company site said it took less than 30 minutes to assemble the chassis by hand.
George Anders in Forbes said, "when it comes to the chassis, Czinger's Divergent Microfactories is taking a much more audacious approach than simply fusing plastic resin."
What does the company mean by nodes?
"Nodes are the key building block we developed to build cars," according to the company. "They are made of a metal alloy and are produced using 3D printers. The nodes combined with carbon fiber tubes are the key components in building a car chassis."
The company said the weight of the Node-enabled chassis is up to 90 percent lighter than traditional cars. What kinds of cars could be built with their technology? Anything, they answered, from a two-seat sports car to a pickup.
More information: www.divergentmicrofactories.com/
© 2015 Tech Xplore