Taking cue from nature, researchers design machines that bend
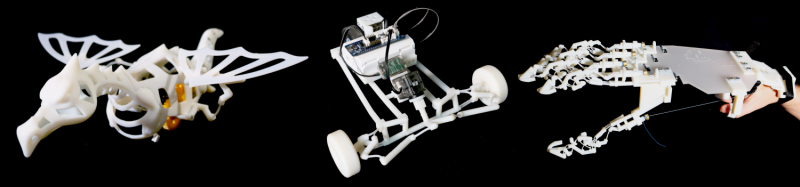
Replacing rigid joints and linkages with mechanisms that bend offers a number of potential advantages, even as it makes designing devices more difficult. A computational design tool developed by Disney Research promises to make this transition from rigid to compliant mechanisms easier.
The tool can take a design for a conventional, rigidly articulated device and automatically substitute parts that achieve the same function through flexibility, drawing from existing catalogs of compliant mechanisms.
"Compliant mechanisms enjoy widespread use in industry - ranging from miniature actuators in microelectromechanical systems to the binder clips, backpack latches and shampoo lids common in everyday life," said Bernhard Thomaszewski, a former Disney scientist who is now an assistant professor at the University of Montreal. "Even broader use in machines is attractive because of their precision and because they can be readily manufactured."
"Unfortunately, designing for flexibility is more difficult than for rigidity because it demands a deeper understanding of how materials behave as their shape changes," added Moritz Bacher, a research scientist at Disney Research.
Thomaszewski, Bacher and their colleagues will present their new method at SIGGRAPH 2017, the Computer Graphics and Interactive Techniques Conference, beginning July 30 in Los Angeles.
"Rigidity is a concept foreign to the living world," said Markus Gross, vice president at Disney Research. "From a kangaroo's legs to the wings of a bat, bones, tendons and cartilage are the nuts and bolts of organic machines. Our research team has developed a tool that will make it easier for us to eventually make our machines as efficient and robust as those we find in nature."
"With its ability to create complex geometry using a variety of strong and flexible materials, 3D printing is an ideal way to manufacture these compliant mechanisms," said Stelian Coros, assistant professor at Carnegie Mellon University. The researchers demonstrated their methods by 3D-printing several mechanisms, including the steering mechanism for a toy car, a compliant hand and a multi-jointed leg mechanism known as Jansen's Linkage.
The design tool replaced conventional joints and linkages with compliant versions, with the exception of hinge joints that rotate more than 360 degrees, for which there is no compliant substitute. The tool then optimizes the performance of the device, modifying the design as necessary to achieve lateral stability, eliminate instances where joint components might collide during use and reduce strains that would cause a component to break.
This process also ensures that the device performs as intended, such as achieving a desired gait with a leg assembly. The tool favors robustness in design, though sometimes that comes at the expense of performance accuracy.
In addition to Thomaszewski, Bacher, Gross and Coros, the research team included Vittorio Megaro from ETH Zurich and Jonas Zehnder.
Combining creativity and innovation, this research continues Disney's rich legacy of leveraging technology to enhance the tools and systems of tomorrow.
More information: "A Computational Design Tool for Compliant Mechanisms-Paper" [PDF, 1.21 MB]